ROBOTRAX® System
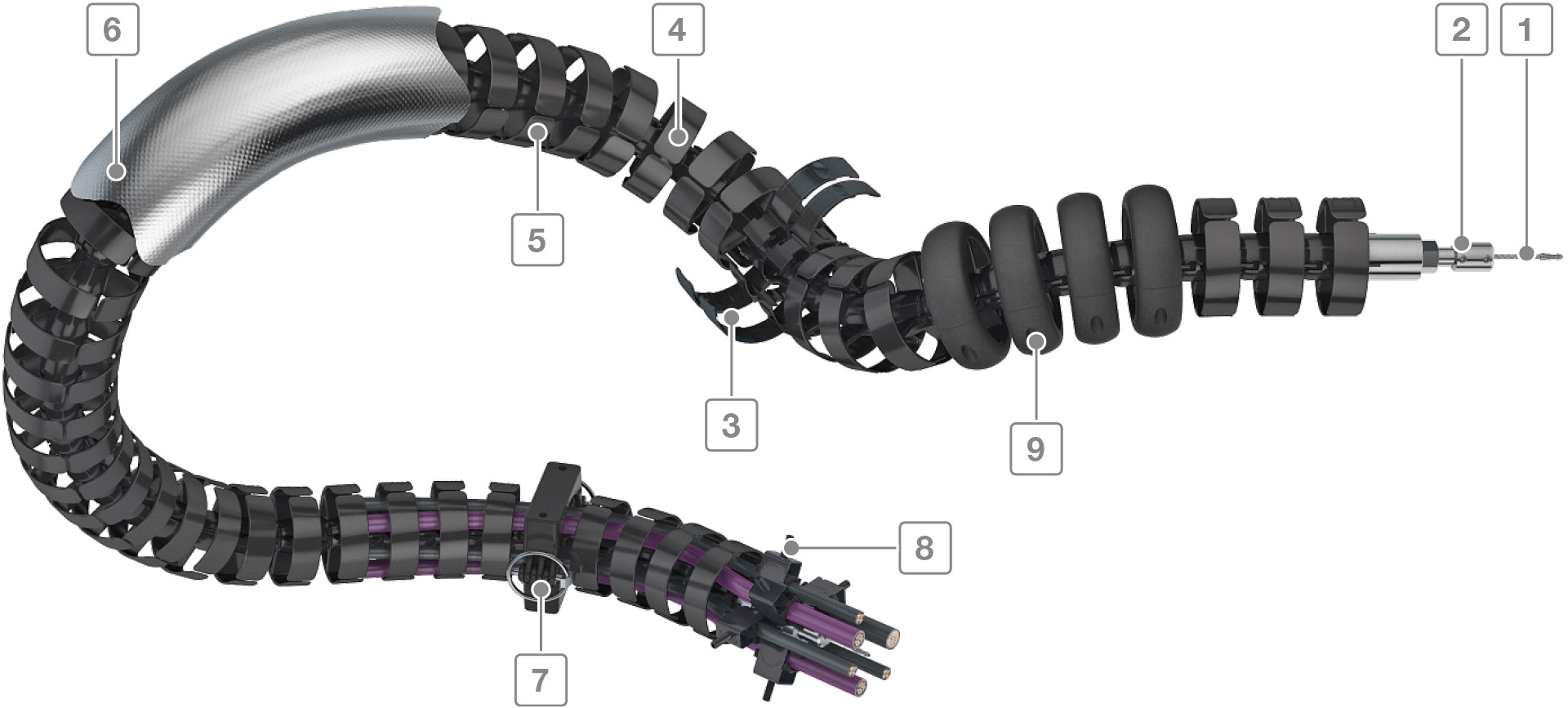
Features
- Suitable for three-dimensional swivel and rotation movements
- Ideal for a long service life of the cables:
– The bending radius does not fall below the minimum when using protectors
– The cables can be separated in three chambers - Also ideal for turntables
Chain links single part
The basic structure of ROBOTRAX® consists of plastic links. These have spherical snap-on connections on both sides. This allows the individual links to be snapped together to form a cable carrier.
Protectors ensure that the bending radius does not fall below the minimum in any direction. The links can be rotated in the radial direction (see table values). The cables can be separated in three chambers.
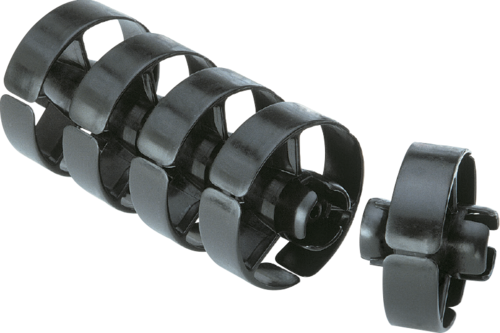
Chain links with crossbars
The basic construction is similar to the ROBOTRAX® types with single part design. Swiveling crossbars with snap locks make it easy to open and safely close the cable carrier. In addition, the three chambers can be divided horizontally and vertically by a divider module for precisely separating cables and hoses.
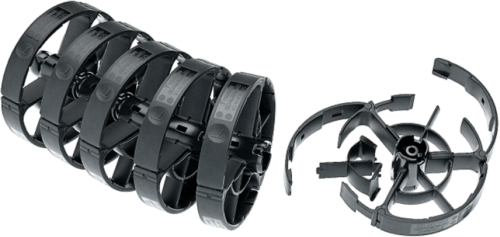
Mounting kit
Fast movements of the robot arms generate high accelerations and therefore high tensile forces on the cable carrier. To transfer these tensile forces, ROBOTRAX® has a hole at the center of each chain link through which the steel cable is pulled. This steel cable takes on the function of force transmission.
The steel cable is fixed with a clamping piece on one side. ROBOTRAX® permits accelerations up to 10 g.
The clamping piece can be used to easily set the chain links to the desired tension and adjust them at any time.
Long service life of the cables and hoses:
The forces are primarily transmitted by the cable carrier and not by cables and hoses.
The mounting set consists of steel cable, clamping and tension piece for up to 5 m cable carrier length.
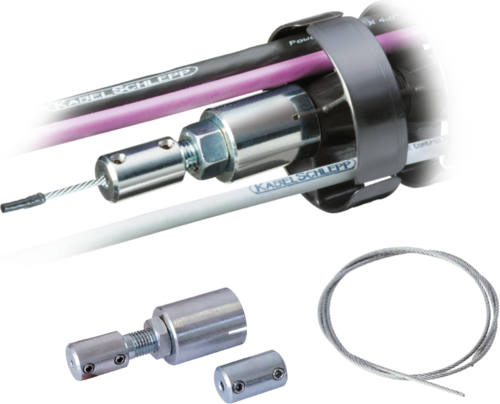
Quick-release brackets
The ROBOTRAX® is fixed and continued with quick-release brackets which are attached with screws. The quick-release brackets fit on any chain link of the respective size. This means the fixing points can be individually adjusted to the motion sequence.
Locking bolt:
100% recyclable, cost-effective locking bolt, optimized for installation space and environment. The bolt can be assembled and disassembled without tools.
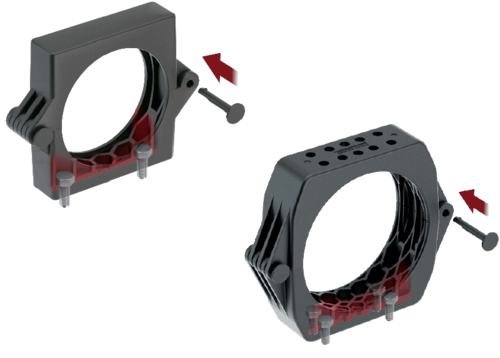
Heat shield/protective cover
Heat shield: The heat shield made from aluminum-coated textile fibers protects the ROBOTRAX® system and inserted cables against flying sparks, weld spatter and radiated heat.
Protective cover: The protective cover made from coated polyester protects against aggressive cutting fluids, hydraulic oils, fine dust and paint spatter.
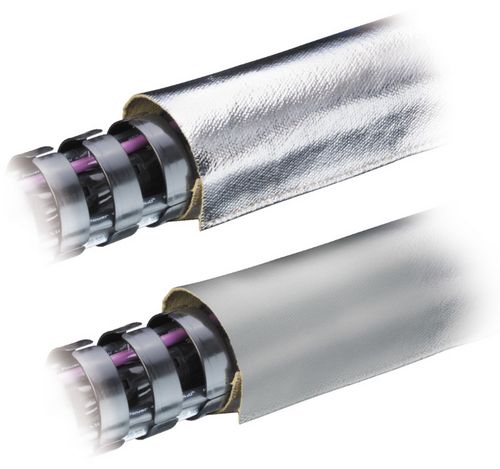
Strain relief for cable ties
(available for all types)
For secure fixing of the cables.
The strain relief can be used on either end.
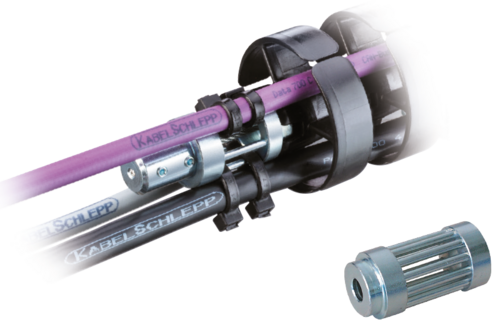
Strain relief LFR
(for types R075, R085, R100 and R140X)
Secure cable fixing, gentle on the cables.
Multi-layer cable fixing is also possible with double and triple LineFix® clamps. Several systems can be installed in sequence.
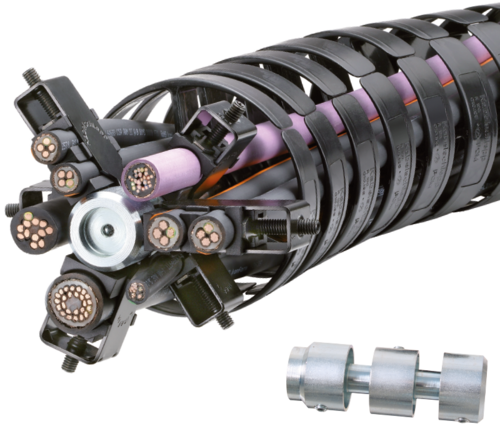
PBU pull back unit
(for types R040, R056, R075, R085 and R100)
PBU: With fast movement sequences and large work envelopes, the relatively long carriers knock against the robot arm. The repeated impact significantly reduces the service life of the cable carrier and the cables within, and the entire system can fail. Downtimes cause high costs and problems in the manufacturing process – so they have to be avoided.
- Compact design: fewer interfering contours and lower risk of collision
- Maximum flexibility for cable carrier routing
- No maintenance on the retraction element required
- Standard mounting for KUKA, ABB and FANUC
PBU is available for new robots, regardless of size, manufacturer, type or application, as well as retrofits and upgrades for existing workcells. It can be mounted vertically, horizontally or upside down. The extension length of the LSH 3 is 350 mm.
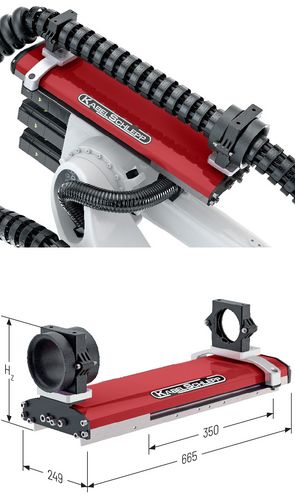
Protector
The service life of the cable carriers and cables is significantly reduced by impact during fast movement sequences and in large work envelopes. The Protector protects the cable carrier against hard impacts, excessive abrasion and premature wear, while also acting as a limitation for the smallest bending radius. Downtimes are minimized. Not the entire cable carrier has to be replaced, but only the Protector in some cases.
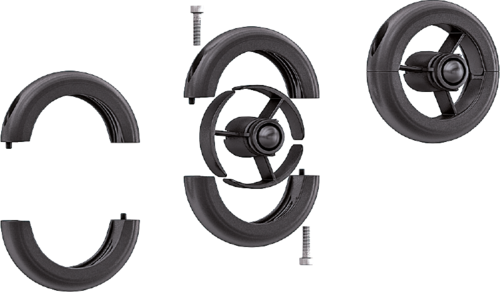
Turntable for quick-release bracket
One additional degree of freedom on the attachments points. When mounted on a turntable, the quick-release bracket can rotate as well, to offer increased flexibility during complex robot movements.
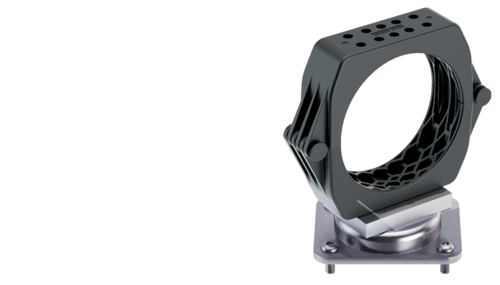
Coil spring for quick-release bracket
If the quick-release bracket is mounted on a coil spring, it can move elastically in all directions, deflect in 3 dimensions and spring back.
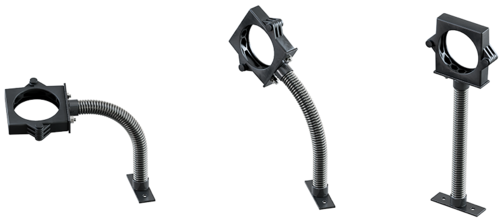
Cobot holder
(for types R040 and R056)
The ROBOTRAX® cobot holder was specially developed for sizes R040 and R056 as well as for corrugated tubes from the FIPLOCK® series (23-48). As a high-quality solution for industrial use, the sturdy steel straps offer non-slip support up to 100 N centrifugal force and thus ensure the trouble-free function of the cobot and the attached cables and hoses in continuous operation. It can be mounted on various surfaces and on diameters between 50-130 mm.
The anti-twist design, an easily accessible lock and a protective rubber profile provide additional safety and support.
The cobot holder is versatile - from handling and quality assurance, assembly and laboratory automation to logistics, medical technology and service robotics - and ensures precision, safety and efficiency.
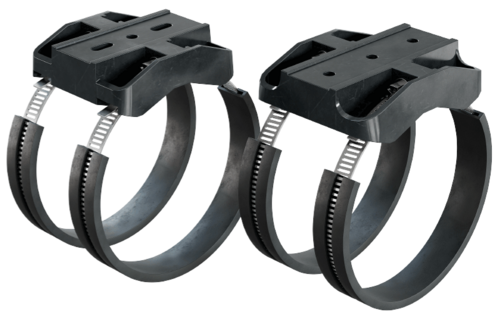
R040 Order no. Set | R056 Order no. Set | |
Set for Ø 50-70 mm | 60552 | 60556 |
Set for Ø 70-90 mm | 60553 | 60557 |
Set for Ø 90-110 mm | 60554 | 60558 |
Set for Ø 110-130 mm | 60555 | 60559 |